The product has high requirements for flatness, contour, and mounting hole position accuracy. High-precision forming process capabilities and large-size product CMM detection capabilities are required to achieve production
It involves multiple processes such as blanking, stacking, welding, forming, trimming, and grinding. It requires joint design by senior technicians in various process fields to provide a mature process solution.
Copper busbars are essential components in power distribution systems and can provide reliable and efficient conduction methods for various applications. Copper busbars are made of highly conductive materials such as copper or aluminum, and are designed to reduce system losses and improve the performance of power distribution networks.
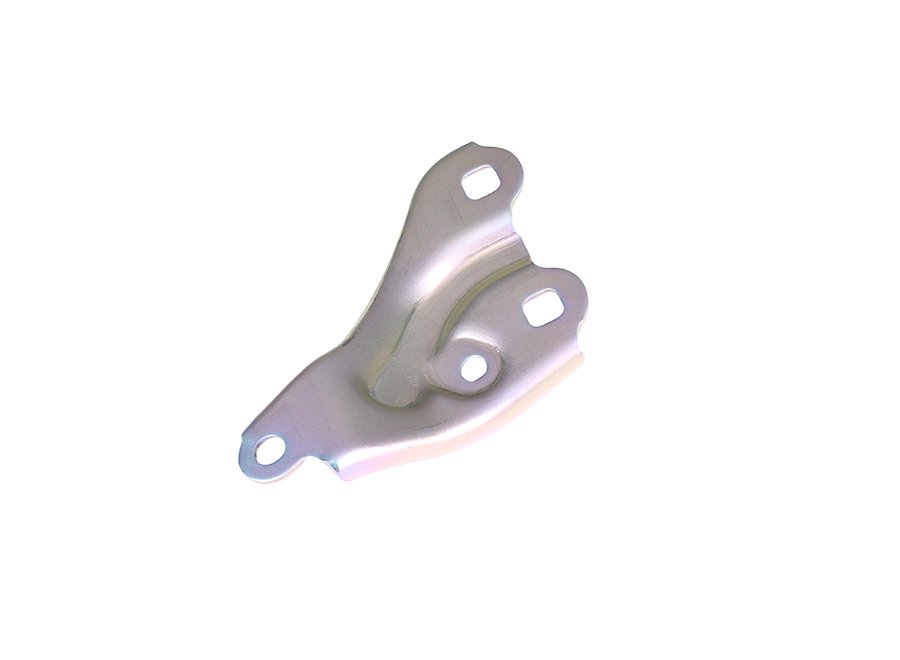
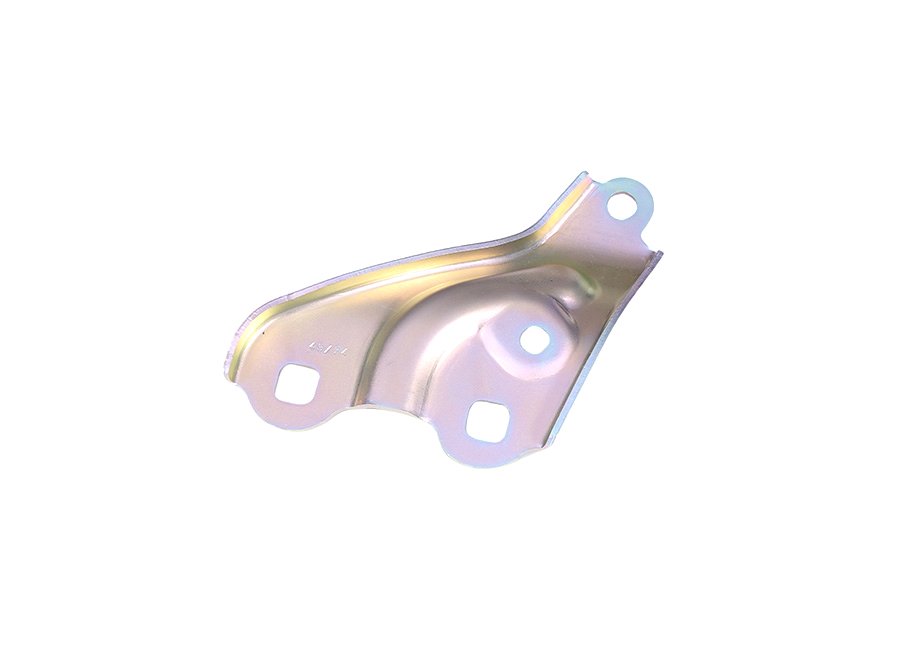
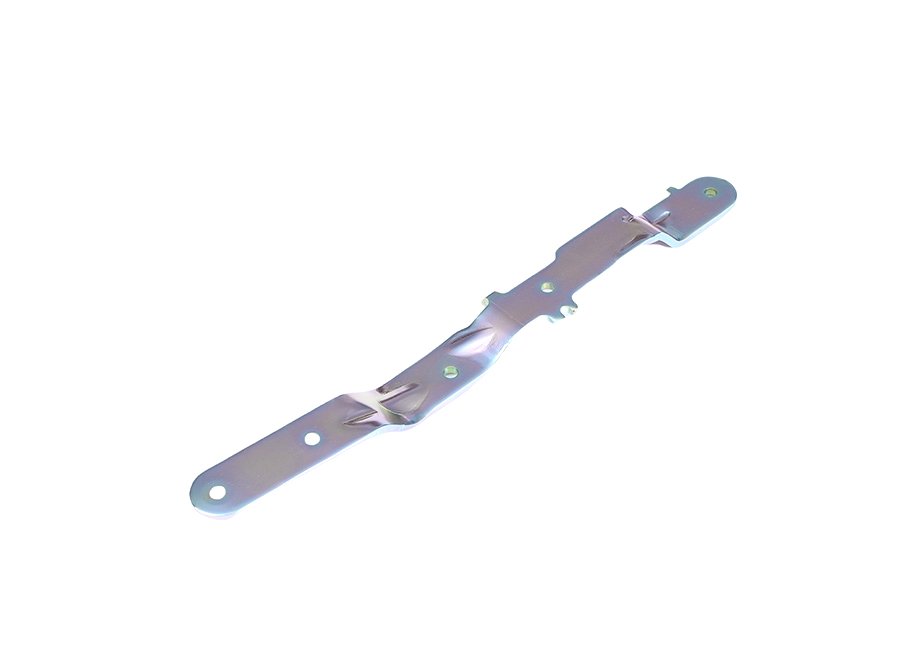
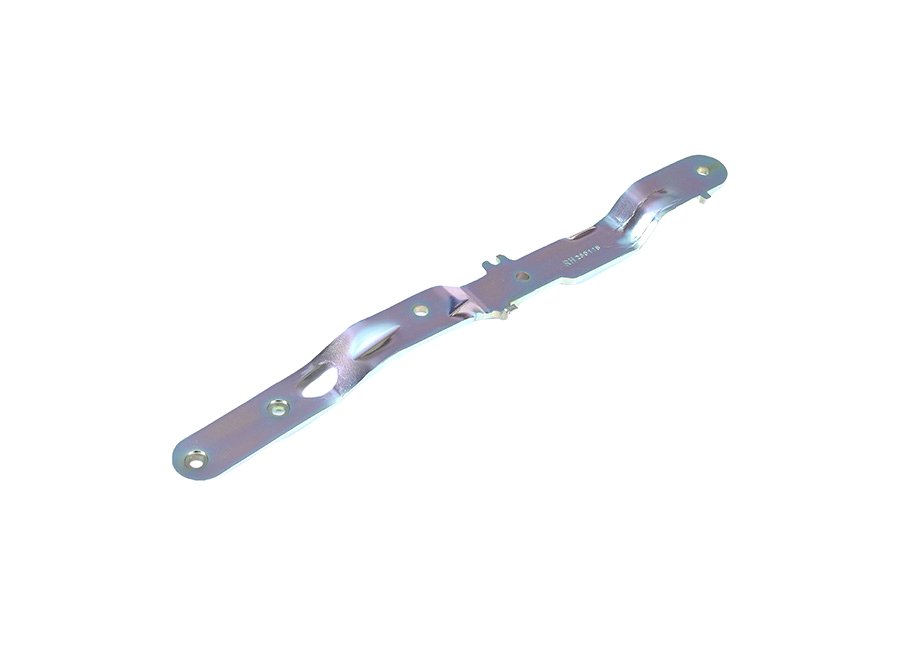

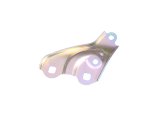
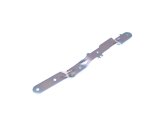
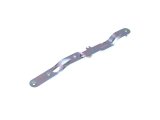
Dipping Aluminium Busbar
Highlights at a glance:
Inquiry Now
add to cart
-
Product Details
-
related products
-
Inquiry Now
Product Details
Materials: T2/TU1 COPPER、AL1060、AL6101、heat shrink tubing、PVC、EVA、PA、PI
Processes:injection molding, dip molding, casing, spraying, extrusion thermoforming
Max. Temperature Resistance:Class 900°C (3H)
Surface treatment:Tin, Ni, Au, Silver plating
These busbars are widely used in electric vehicles (EVs), battery energy storage systems (BESS), and solar inverter cabinets. The aluminum core ensures lightweight properties, while the dipping process gives a clean, uniform coating for safe, space-saving installations.